SteelMPF - Menegotto and Pinto (1973) Model Extended by Filippou et al. (1983): Difference between revisions
Kkolozvari (talk | contribs) No edit summary |
Kkolozvari (talk | contribs) No edit summary |
||
Line 60: | Line 60: | ||
Furthermore, it has been observed from the strain-stress relationships obtained from quasi-static or dynamic analyses using existing steel models in OpenSees (e.g., '''Steel02''') that after partial unloading occurs in a model element caused by dynamic loading or stress re-distribution under quasi-static loading due to concrete cracking or crushing, the Menegotto-Pinto formulation produces stress overshooting in the cyclic stress-strain behavior of reinforcing steel. This overshooting effect is not behavioral and causes non-physical hardening in the stress–strain behavior, upon reloading from the partial unloading loop. This phenomenon is illustrated in Figure 3 for the '''Steel02''' model in OpenSees. This anomaly results in overestimation of steel stresses predicted by the '''Steel02''' model upon return from partial unloading, yielding strain–stress curve that may not represent the physical constitutive behavior of reinforcing steel under cyclic loading. This limitation in the Menegotto-Pinto model formulation has also been acknowledged by Filippou et al. (1983). | Furthermore, it has been observed from the strain-stress relationships obtained from quasi-static or dynamic analyses using existing steel models in OpenSees (e.g., '''Steel02''') that after partial unloading occurs in a model element caused by dynamic loading or stress re-distribution under quasi-static loading due to concrete cracking or crushing, the Menegotto-Pinto formulation produces stress overshooting in the cyclic stress-strain behavior of reinforcing steel. This overshooting effect is not behavioral and causes non-physical hardening in the stress–strain behavior, upon reloading from the partial unloading loop. This phenomenon is illustrated in Figure 3 for the '''Steel02''' model in OpenSees. This anomaly results in overestimation of steel stresses predicted by the '''Steel02''' model upon return from partial unloading, yielding strain–stress curve that may not represent the physical constitutive behavior of reinforcing steel under cyclic loading. This limitation in the Menegotto-Pinto model formulation has also been acknowledged by Filippou et al. (1983). | ||
[[File: | [[File:Steel_MPF_02.png|500px|thumb|center|Figure 3. Comparison of Steel02 and SteelMPF]] | ||
The overshooting effect observed in the existing OpenSees material model for reinforcing steel (e.g., '''Steel02''') has been remedied in '''SteelMPF''', via manipulating the model formulation so that reloading behavior after partial unloading cannot overshoot the previous loading loop in the cyclic stress-strain behavior. The comparison between strain–stress relationships obtained using '''SteelMPF''' and '''Steel02''' for a strain history that includes low-amplitude unloading followed by reloading is presented in Figure 3. | The overshooting effect observed in the existing OpenSees material model for reinforcing steel (e.g., '''Steel02''') has been remedied in '''SteelMPF''', via manipulating the model formulation so that reloading behavior after partial unloading cannot overshoot the previous loading loop in the cyclic stress-strain behavior. The comparison between strain–stress relationships obtained using '''SteelMPF''' and '''Steel02''' for a strain history that includes low-amplitude unloading followed by reloading is presented in Figure 3. |
Revision as of 04:46, 13 January 2016
- Command_Manual
- Tcl Commands
- Modeling_Commands
- model
- uniaxialMaterial
- ndMaterial
- frictionModel
- section
- geometricTransf
- element
- node
- sp commands
- mp commands
- timeSeries
- pattern
- mass
- block commands
- region
- rayleigh
- Analysis Commands
- Output Commands
- Misc Commands
- DataBase Commands
Developed and Implemented by:
Kristijan Kolozvari, California State University, Fullerton
Kutay Orakcal, Bogazici University, Istanbul, Turkey
John Wallace, Univeristy of California, Los Angeles
This command is used to construct a uniaxialMaterial SteelMPF, which represents the well-known uniaxial constitutive nonlinear hysteretic material model for steel proposed by Menegotto and Pinto (1973), and extended by Filippou et al. (1983) to include isotropic strain hardening effects. The relationship is in the form of curved transitions (Figure 1), each from a straight-line asymptote with slope E0 (modulus of elasticity) to another straight-line asymptote with slope E1 = bE0 (yield modulus) where b is the strain hardening ratio. The curvature of the transition curve between the two asymptotes is governed by a cyclic curvature parameter R, which permits the Bauschinger effect to be represented, and is dependent on the absolute strain difference between the current asymptote intersection point and the previous maximum or minimum strain reversal point depending on whether the current strain is increasing or decreasing, respectively. The strain and stress pairs (εr,σr) and (ε0,σ0) shown on Figure 1 are updated after each strain reversal.
Source: /usr/local/cvs/OpenSees/SRC/material/uniaxial/
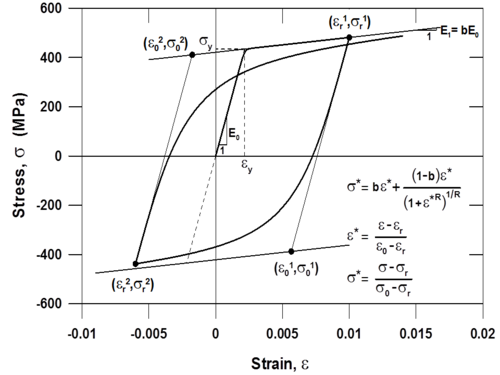
Input Format:
uniaxialMaterial SteelMPF $mattag $fyp $fyn $E0 $bp $bn $R0 $a1 $a2 <$a3 $a4> |
$mattag | Unique uniaxialMaterial tag |
$fyp | Yield strength in tension (positive loading direction) |
$fyn | Yield strength in compression (negative loading direction) |
$E0 | Initial tangent modulus |
$bp | Strain hardening ratio in tension (positive loading direction) |
$bn | Strain hardening ratio in compression (negative loading direction) |
$R0 | Initial value of the curvature parameter R (R0 = 20 recommended) |
$a1 | Curvature degradation parameter (a1 = 18.5 recommended) |
$a2 | Curvature degradation parameter (a2 = 0.15 or 0.0015 recommended) |
$a3 | Isotropic hardening parameter (optional, default = 0.01) |
$a4 | Isotropic hardening parameter (optional, default = 7.0) |
Example:
uniaxialMaterial SteelMPF 1 60 60 29000 0.02 0.02 20.0 18.5 0.15
Discussion:
Although the Menegotto-Pinto model is already available in OpenSees (e.g., Steel02), the formulation of SteelMPF introduces several distinctive features compared to existing models. For example, the model allows definition of different yield stress values and strain hardening ratios for tension and compression, and it considers degradation of cyclic curvature parameter R for strain reversals in both pre- and post- yielding regions, which could produce more accurate predictions of yield capacity for some RC wall specimens (element MVLEM, Example 1), whereas Steel02 considers the degradation in post-yielding region only. Strain-stress relationships obtained using SteelMPF and Steel02 are compared in Figure 2 for a strain history that includes strain reversals at strain values equal to one-half of the yield strain (i.e., εr = ±0.001 = εy/2). The model also allows calibration of isotropic hardening parameters through optional input variables a3 and a4, and uses default values of a3 = 0.01 and a4 = 7.0 as calibrated by Filippou et al. (1983) based on test results. To disregard isotropic strain hardening behavior in SteelMPF, parameter a3 needs to be assigned a zero value (a3 = 0.0).
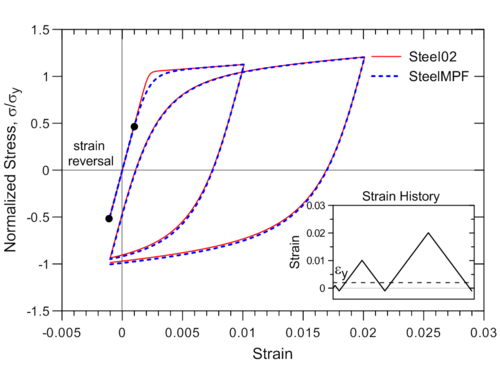
Furthermore, it has been observed from the strain-stress relationships obtained from quasi-static or dynamic analyses using existing steel models in OpenSees (e.g., Steel02) that after partial unloading occurs in a model element caused by dynamic loading or stress re-distribution under quasi-static loading due to concrete cracking or crushing, the Menegotto-Pinto formulation produces stress overshooting in the cyclic stress-strain behavior of reinforcing steel. This overshooting effect is not behavioral and causes non-physical hardening in the stress–strain behavior, upon reloading from the partial unloading loop. This phenomenon is illustrated in Figure 3 for the Steel02 model in OpenSees. This anomaly results in overestimation of steel stresses predicted by the Steel02 model upon return from partial unloading, yielding strain–stress curve that may not represent the physical constitutive behavior of reinforcing steel under cyclic loading. This limitation in the Menegotto-Pinto model formulation has also been acknowledged by Filippou et al. (1983).
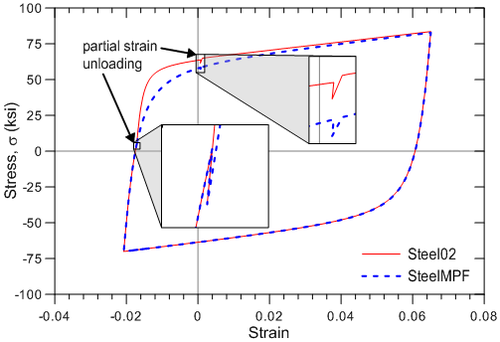
The overshooting effect observed in the existing OpenSees material model for reinforcing steel (e.g., Steel02) has been remedied in SteelMPF, via manipulating the model formulation so that reloading behavior after partial unloading cannot overshoot the previous loading loop in the cyclic stress-strain behavior. The comparison between strain–stress relationships obtained using SteelMPF and Steel02 for a strain history that includes low-amplitude unloading followed by reloading is presented in Figure 3.
References:
1) Filippou F.C., Popov, E.P., and Bertero, V.V. (1983). "Effects of Bond Deterioration on Hysteretic Behavior of Reinforced Concrete Joints". Report EERC 83-19, Earthquake Engineering Research Center, University of California, Berkeley.
2) Menegotto, M., and Pinto, P.E. (1973). Method of analysis of cyclically loaded RC plane frames including changes in geometry and non-elastic behavior of elements under normal force and bending. Preliminary Report IABSE, vol 13.