FSAM - 2D RC Panel Constitutive Behavior: Difference between revisions
Kkolozvari (talk | contribs) No edit summary |
Kkolozvari (talk | contribs) No edit summary |
||
(5 intermediate revisions by the same user not shown) | |||
Line 3: | Line 3: | ||
'''Developed and Implemented by:''' | '''Developed and Implemented by:''' | ||
<span style="color:blue"> Kristijan Kolozvari<span style="color:black">, California State University, Fullerton | [mailto:kkolozvari@fullerton.edu <span style="color:blue"> Kristijan Kolozvari<span style="color:black">], California State University, Fullerton | ||
<span style="color:blue"> Kutay Orakcal<span style="color:black">, Bogazici University, Istanbul, Turkey | <span style="color:blue"> Kutay Orakcal<span style="color:black">, Bogazici University, Istanbul, Turkey | ||
Line 11: | Line 11: | ||
<span style="color:blue"> John Wallace<span style="color:black">, Univeristy of California, Los Angeles | <span style="color:blue"> John Wallace<span style="color:black">, Univeristy of California, Los Angeles | ||
This command is used to construct a nDMaterial '''FSAM''' (Fixed-Strut-Angle-Model, Figure 1), which is a plane-stress constitutive model for simulating the behavior of RC panel elements under generalized, in-plane, reversed-cyclic loading conditions (Ulugtekin, 2010; Orakcal et al., 2012). In the '''FSAM''' constitutive model, the strain fields acting on concrete and reinforcing steel components of a RC panel are assumed to be equal to each other, implying perfect bond assumption between concrete and reinforcing steel bars. While the reinforcing steel bars develop uniaxial stresses under strains in their longitudinal direction, the behavior of concrete is defined using stress–strain relationships in biaxial directions, the orientation of which is governed by the state of cracking in concrete. Although the concrete stress–strain relationship used in the '''FSAM''' is fundamentally uniaxial in nature, it also incorporates biaxial softening effects including compression softening and biaxial damage. For transfer of shear stresses across the cracks, a friction-based elasto-plastic shear aggregate interlock model is adopted, together with a linear elastic model for representing dowel action on the reinforcing steel bars (Kolozvari, 2013). Note that '''FSAM''' constitutive model is implemented to be used with Shear-Flexure Interaction model for RC walls ([http://opensees.berkeley.edu/wiki/index.php/SFI_MVLEM_-_Cyclic_Shear-Flexure_Interaction_Model_for_RC_Walls '''SFI_MVLEM''') | This command is used to construct a nDMaterial '''FSAM''' (Fixed-Strut-Angle-Model, Figure 1, Kolozvari et al., 2015), which is a plane-stress constitutive model for simulating the behavior of RC panel elements under generalized, in-plane, reversed-cyclic loading conditions (Ulugtekin, 2010; Orakcal et al., 2012). In the '''FSAM''' constitutive model, the strain fields acting on concrete and reinforcing steel components of a RC panel are assumed to be equal to each other, implying perfect bond assumption between concrete and reinforcing steel bars. While the reinforcing steel bars develop uniaxial stresses under strains in their longitudinal direction, the behavior of concrete is defined using stress–strain relationships in biaxial directions, the orientation of which is governed by the state of cracking in concrete. Although the concrete stress–strain relationship used in the '''FSAM''' is fundamentally uniaxial in nature, it also incorporates biaxial softening effects including compression softening and biaxial damage. For transfer of shear stresses across the cracks, a friction-based elasto-plastic shear aggregate interlock model is adopted, together with a linear elastic model for representing dowel action on the reinforcing steel bars (Kolozvari, 2013). Note that '''FSAM''' constitutive model is implemented to be used with Shear-Flexure Interaction model for RC walls ([http://opensees.berkeley.edu/wiki/index.php/SFI_MVLEM_-_Cyclic_Shear-Flexure_Interaction_Model_for_RC_Walls '''SFI_MVLEM''']), but it could be also used elsewhere. | ||
'''Source:''' /usr/local/cvs/OpenSees/SRC/material/nD/reinforcedConcretePlaneStress/ | '''Source:''' /usr/local/cvs/OpenSees/SRC/material/nD/reinforcedConcretePlaneStress/ | ||
Line 46: | Line 46: | ||
<sup class="superscript">1</sup>nDMaterial '''FSAM''' shall be used with uniaxialMaterial [http://opensees.berkeley.edu/wiki/index.php/ConcreteCM_-_Complete_Concrete_Model_by_Chang_and_Mander_(1994) '''ConcreteCM'''] | <sup class="superscript">1</sup>nDMaterial '''FSAM''' shall be used with uniaxialMaterial [http://opensees.berkeley.edu/wiki/index.php/ConcreteCM_-_Complete_Concrete_Model_by_Chang_and_Mander_(1994) '''ConcreteCM'''] | ||
Recommended values for parameter of a shear resisting mechanism ('''nu''' and '''alfadow''', Figure 2) are provided above. Details about the sensitivity of analytical predictions using '''SFI_MVLEM''' to changes in these parameters are presented by Kolozvari (2013). | Recommended values for parameter of a shear resisting mechanism ('''nu''' and '''alfadow''', Figure 2) are provided above. Details about the sensitivity of analytical predictions using [http://opensees.berkeley.edu/wiki/index.php/SFI_MVLEM_-_Cyclic_Shear-Flexure_Interaction_Model_for_RC_Walls '''SFI_MVLEM'''] element to changes in these parameters are presented by Kolozvari (2013). | ||
---- | ---- | ||
Line 54: | Line 54: | ||
{| | {| | ||
| style="width:150px" | '''panel_strain''' || Strains ε<sub class="subscript">x</sub>, ε<sub class="subscript">y</sub>, γ<sub class="subscript">xy</sub> (Figure | | style="width:150px" | '''panel_strain''' || Strains ε<sub class="subscript">x</sub>, ε<sub class="subscript">y</sub>, γ<sub class="subscript">xy</sub> (Figure 1) | ||
|- | |- | ||
|'''panel_stress''' || Resulting panel stresses σ<sub class="subscript">x</sub>, σ<sub class="subscript">y</sub>, τ<sub class="subscript">xy</sub> (concrete and steel, Figure 1) | |'''panel_stress''' || Resulting panel stresses σ<sub class="subscript">x</sub>, σ<sub class="subscript">y</sub>, τ<sub class="subscript">xy</sub> (concrete and steel, Figure 1) | ||
Line 60: | Line 60: | ||
| '''panel_stress_concrete''' || Resulting panel concrete stresses σ<sub class="subscript">xc</sub>, σ<sub class="subscript">yc</sub>, τ<sub class="subscript">xyc</sub> (Figure 2b) | | '''panel_stress_concrete''' || Resulting panel concrete stresses σ<sub class="subscript">xc</sub>, σ<sub class="subscript">yc</sub>, τ<sub class="subscript">xyc</sub> (Figure 2b) | ||
|- | |- | ||
| '''panel_stress_steel''' ||Resulting panel steel stresses σ<sub class="subscript">xs</sub>, σ<sub class="subscript">ys</sub>, τ<sub class="subscript">xys</sub> (Figure | | '''panel_stress_steel''' ||Resulting panel steel stresses σ<sub class="subscript">xs</sub>, σ<sub class="subscript">ys</sub>, τ<sub class="subscript">xys</sub> (Figure 2e) | ||
|- | |- | ||
| '''strain_stress_steelX''' || Uniaxial strain and stress of horizontal reinforcement ε<sub class="subscript">x</sub>, σ<sub class="subscript">xxs</sub> | | '''strain_stress_steelX''' || Uniaxial strain and stress of horizontal reinforcement ε<sub class="subscript">x</sub>, σ<sub class="subscript">xxs</sub> (Figure 2f) | ||
|- | |- | ||
| '''strain_stress_steelY''' || Uniaxial strain and stress of vertical reinforcement ε<sub class="subscript">y</sub>, σ<sub class="subscript">yys</sub> | | '''strain_stress_steelY''' || Uniaxial strain and stress of vertical reinforcement ε<sub class="subscript">y</sub>, σ<sub class="subscript">yys</sub> (Figure 2f) | ||
|- | |- | ||
| '''strain_stress_concrete1''' || Uniaxial strain and stress of concrete strut 1 ε<sub class="subscript">c1</sub>, σ<sub class="subscript">c1</sub> | | '''strain_stress_concrete1''' || Uniaxial strain and stress of concrete strut 1 ε<sub class="subscript">c1</sub>, σ<sub class="subscript">c1</sub> (Figure 2c) | ||
|- | |- | ||
| '''strain_stress_concrete2''' || Uniaxial strain and stress of concrete strut 2 ε<sub class="subscript">c2</sub>, σ<sub class="subscript">c2</sub> | | '''strain_stress_concrete2''' || Uniaxial strain and stress of concrete strut 2 ε<sub class="subscript">c2</sub>, σ<sub class="subscript">c2</sub> (Figure 2c) | ||
|- | |- | ||
| '''strain_stress_interlock1''' || Shear strain and stress in concrete along crack 1 ε<sub class="subscript">cr1</sub>, τ<sub class="subscript">cr1</sub> (Figure | | '''strain_stress_interlock1''' || Shear strain and stress in concrete along crack 1 ε<sub class="subscript">cr1</sub>, τ<sub class="subscript">cr1</sub> (Figure 2d) | ||
|- | |- | ||
| '''strain_stress_interlock2''' || Shear strain and stress in concrete along crack 2 ε<sub class="subscript">cr2</sub>, τ<sub class="subscript">cr2</sub> (Figure | | '''strain_stress_interlock2''' || Shear strain and stress in concrete along crack 2 ε<sub class="subscript">cr2</sub>, τ<sub class="subscript">cr2</sub> (Figure 2d) | ||
|- | |- | ||
| '''cracking_angles''' || Orientation of concrete cracks | | '''cracking_angles''' || Orientation of concrete cracks | ||
|} | |} | ||
Note that recorders for a RC panel (marco-fiber) are invoked as '''SFI_MVLEM''' element recorders using command '''RCPanel''' and one of the desired commands listed above. Currently, it is possible to output values only for one macro-fiber within one or multiple elements. | Note that recorders for a RC panel (marco-fiber) are invoked as [http://opensees.berkeley.edu/wiki/index.php/SFI_MVLEM_-_Cyclic_Shear-Flexure_Interaction_Model_for_RC_Walls '''SFI_MVLEM'''] element recorders using command '''RCPanel''' and one of the desired commands listed above. Currently, it is possible to output values only for one macro-fiber within one or multiple elements. | ||
---- | ---- | ||
Line 86: | Line 86: | ||
Recorder Element -file MVLEM_panel_strain.out -time -ele 1 RCPanel 1 panel_strain | Recorder Element -file MVLEM_panel_strain.out -time -ele 1 RCPanel 1 panel_strain | ||
[[File: | [[File:FSAM_2a.png|1000px|thumb|center|Figure 2. Behavior and Input/Output Parameters of the FSAM Constitutive Model]] | ||
---- | ---- | ||
'''References:''' | '''References:''' | ||
1) Kolozvari K. ( | 1) Kolozvari K., Orakcal K., and Wallace J. W. (2015). "Shear-Flexure Interaction Modeling of reinforced Concrete Structural Walls and Columns under Reversed Cyclic Loading", Pacific Earthquake Engineering Research Center, University of California, Berkeley, [http://peer.berkeley.edu/publications/peer_reports/reports_2015/webPEER-2015-12-kolozvari.pdf PEER Report No. 2015/12] | ||
2) | 2) Kolozvari K. (2013). “Analytical Modeling of Cyclic Shear-Flexure Interaction in Reinforced Concrete Structural Walls”, PhD Dissertation, University of California, Los Angeles. | ||
3) Ulugtekin D. (2010). “Analytical Modeling of Reinforced Concrete Panel Elements under Reversed Cyclic Loadings”, M.S. Thesis, Bogazici University, Istanbul, Turkey. | 3) Orakcal K., Massone L.M., and Ulugtekin D. (2012). “Constitutive Modeling of Reinforced Concrete Panel Behavior under Cyclic Loading”, Proceedings, 15th World Conference on Earthquake Engineering, Lisbon, Portugal. | ||
4) Ulugtekin D. (2010). “Analytical Modeling of Reinforced Concrete Panel Elements under Reversed Cyclic Loadings”, M.S. Thesis, Bogazici University, Istanbul, Turkey. |
Latest revision as of 01:56, 13 March 2016
- Command_Manual
- Tcl Commands
- Modeling_Commands
- model
- uniaxialMaterial
- ndMaterial
- frictionModel
- section
- geometricTransf
- element
- node
- sp commands
- mp commands
- timeSeries
- pattern
- mass
- block commands
- region
- rayleigh
- Analysis Commands
- Output Commands
- Misc Commands
- DataBase Commands
Developed and Implemented by:
Kristijan Kolozvari, California State University, Fullerton
Kutay Orakcal, Bogazici University, Istanbul, Turkey
Leonardo Massone, University of Chile, Santiago
John Wallace, Univeristy of California, Los Angeles
This command is used to construct a nDMaterial FSAM (Fixed-Strut-Angle-Model, Figure 1, Kolozvari et al., 2015), which is a plane-stress constitutive model for simulating the behavior of RC panel elements under generalized, in-plane, reversed-cyclic loading conditions (Ulugtekin, 2010; Orakcal et al., 2012). In the FSAM constitutive model, the strain fields acting on concrete and reinforcing steel components of a RC panel are assumed to be equal to each other, implying perfect bond assumption between concrete and reinforcing steel bars. While the reinforcing steel bars develop uniaxial stresses under strains in their longitudinal direction, the behavior of concrete is defined using stress–strain relationships in biaxial directions, the orientation of which is governed by the state of cracking in concrete. Although the concrete stress–strain relationship used in the FSAM is fundamentally uniaxial in nature, it also incorporates biaxial softening effects including compression softening and biaxial damage. For transfer of shear stresses across the cracks, a friction-based elasto-plastic shear aggregate interlock model is adopted, together with a linear elastic model for representing dowel action on the reinforcing steel bars (Kolozvari, 2013). Note that FSAM constitutive model is implemented to be used with Shear-Flexure Interaction model for RC walls (SFI_MVLEM), but it could be also used elsewhere.
Source: /usr/local/cvs/OpenSees/SRC/material/nD/reinforcedConcretePlaneStress/
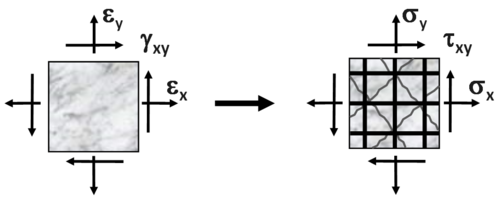
Input Format:
nDMaterial FSAM $mattag $rho $sX $sY $conc $rouX $rouY $nu $alfadow |
$mattag | Unique nDMaterial tag |
$rho | Material density |
$sX | Tag of uniaxialMaterial simulating horizontal (x) reinforcement |
$sY | Tag of uniaxialMaterial simulating vertical (y) reinforcement |
$conc | Tag of uniaxialMaterial1 simulating concrete |
$rouX | Reinforcing ratio in horizontal (x) direction (rouX = As,x/Agross,x) |
$rouY | Reinforcing ratio in vertical (y) direction (rouY = As,y/Agross,y) |
$nu | Concrete friction coefficient (0.0 < nu < 1.5) |
$alfadow | Stiffness coefficient of reinforcement dowel action (0.0 < alfadow < 0.05) |
1nDMaterial FSAM shall be used with uniaxialMaterial ConcreteCM
Recommended values for parameter of a shear resisting mechanism (nu and alfadow, Figure 2) are provided above. Details about the sensitivity of analytical predictions using SFI_MVLEM element to changes in these parameters are presented by Kolozvari (2013).
Material Recorders:
The following output is available from the FSAM RC panel model:
panel_strain | Strains εx, εy, γxy (Figure 1) |
panel_stress | Resulting panel stresses σx, σy, τxy (concrete and steel, Figure 1) |
panel_stress_concrete | Resulting panel concrete stresses σxc, σyc, τxyc (Figure 2b) |
panel_stress_steel | Resulting panel steel stresses σxs, σys, τxys (Figure 2e) |
strain_stress_steelX | Uniaxial strain and stress of horizontal reinforcement εx, σxxs (Figure 2f) |
strain_stress_steelY | Uniaxial strain and stress of vertical reinforcement εy, σyys (Figure 2f) |
strain_stress_concrete1 | Uniaxial strain and stress of concrete strut 1 εc1, σc1 (Figure 2c) |
strain_stress_concrete2 | Uniaxial strain and stress of concrete strut 2 εc2, σc2 (Figure 2c) |
strain_stress_interlock1 | Shear strain and stress in concrete along crack 1 εcr1, τcr1 (Figure 2d) |
strain_stress_interlock2 | Shear strain and stress in concrete along crack 2 εcr2, τcr2 (Figure 2d) |
cracking_angles | Orientation of concrete cracks |
Note that recorders for a RC panel (marco-fiber) are invoked as SFI_MVLEM element recorders using command RCPanel and one of the desired commands listed above. Currently, it is possible to output values only for one macro-fiber within one or multiple elements.
Example:
nDMaterial FSAM 1 0.0 1 2 4 0.0073 0.0606 0.1 0.01
Recorder Element -file MVLEM_panel_strain.out -time -ele 1 RCPanel 1 panel_strain
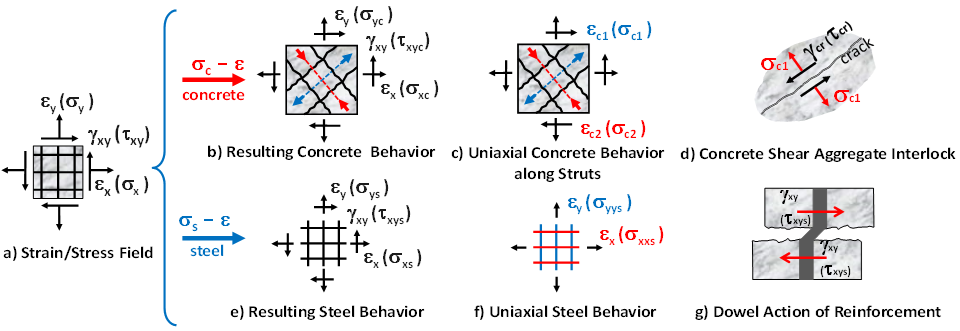
References:
1) Kolozvari K., Orakcal K., and Wallace J. W. (2015). "Shear-Flexure Interaction Modeling of reinforced Concrete Structural Walls and Columns under Reversed Cyclic Loading", Pacific Earthquake Engineering Research Center, University of California, Berkeley, PEER Report No. 2015/12
2) Kolozvari K. (2013). “Analytical Modeling of Cyclic Shear-Flexure Interaction in Reinforced Concrete Structural Walls”, PhD Dissertation, University of California, Los Angeles.
3) Orakcal K., Massone L.M., and Ulugtekin D. (2012). “Constitutive Modeling of Reinforced Concrete Panel Behavior under Cyclic Loading”, Proceedings, 15th World Conference on Earthquake Engineering, Lisbon, Portugal.
4) Ulugtekin D. (2010). “Analytical Modeling of Reinforced Concrete Panel Elements under Reversed Cyclic Loadings”, M.S. Thesis, Bogazici University, Istanbul, Turkey.